The construction of control cabinets and the manufacture of control panels are fundamental components of electrical engineering and automation technology. The increasing complexity of modern production processes and the requirements of Industry 4.0 give rise to numerous challenges - but also opportunities. Digitalization, networking and automation are revolutionizing traditional control cabinet construction.
This article introduces the latest technologies such as IoT, Digital Twin, EPLAN and Perforex milling centers and shows how these innovations influence the entire process - from planning to maintenance.
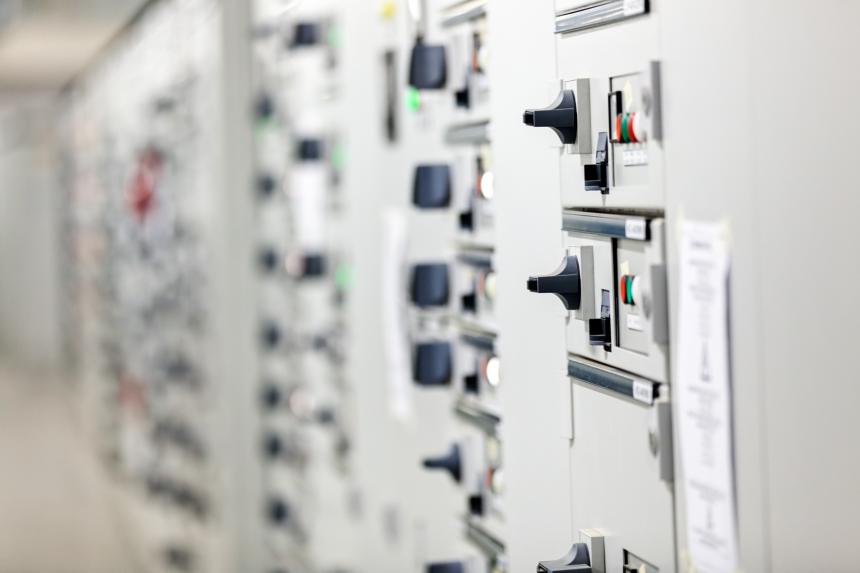
Control cabinets and control panels
Control cabinets
A control cabinet is used to house and protect electrical switching, control and automation components. It contains elements such as fuses, relays, controllers (PLCs) and power supplies that control industrial machines and systems. Traditionally, the focus is on clean wiring and technical standards. But with the introduction of Industry 4.0, aspects such as remote monitoring, real-time data analysis and adaptive control systems are becoming increasingly important.
Control panels
panels Control panels are the interface between man and machine. They consist of control elements such as buttons, switches, displays and selector switches. In addition to ergonomic and safety-related requirements, modern control panels must also offer digital interfaces for IoT-based applications.
Modern technologies in control cabinet construction
Digital Twin in Control Cabinet Construction
The digital twin is a digital representation of a physical system. It is used in control cabinet construction to optimize planning and operation. Engineers can use virtual models to identify design errors, test circuit diagrams and accelerate commissioning. This brings several advantages:
Proactive maintenance: IoT sensors enable real-time monitoring and predictive maintenance.
Optimized design: Weak points can be identified and remedied in advance.
Faster commissioning: Simulations reduce errors and accelerate the process.
Virtual Prototyping
Virtual prototyping involves designing and simulating a control cabinet or system in a digital environment before creating a physical prototype. The aim is to identify design errors early on and shorten development time. It is a purely development-oriented tool that primarily optimizes the planning and design phase. Virtual prototyping therefore focuses on the planning and development phase, while the digital twin creates a permanent connection between the digital and physical worlds and is used for operation and maintenance.
IoT and Industry 4.0 in control cabinet construction
IoT and Industry 4.0 are transforming control cabinet construction into highly networked systems. Smart devices communicate in real time and enable adaptive controls.
Real-time data transmission: Sensors monitor temperature, current and humidity.
Error detection: Problems are identified early and downtime is minimized.
Automated adjustments: Controls react autonomously to current data and optimize processes.
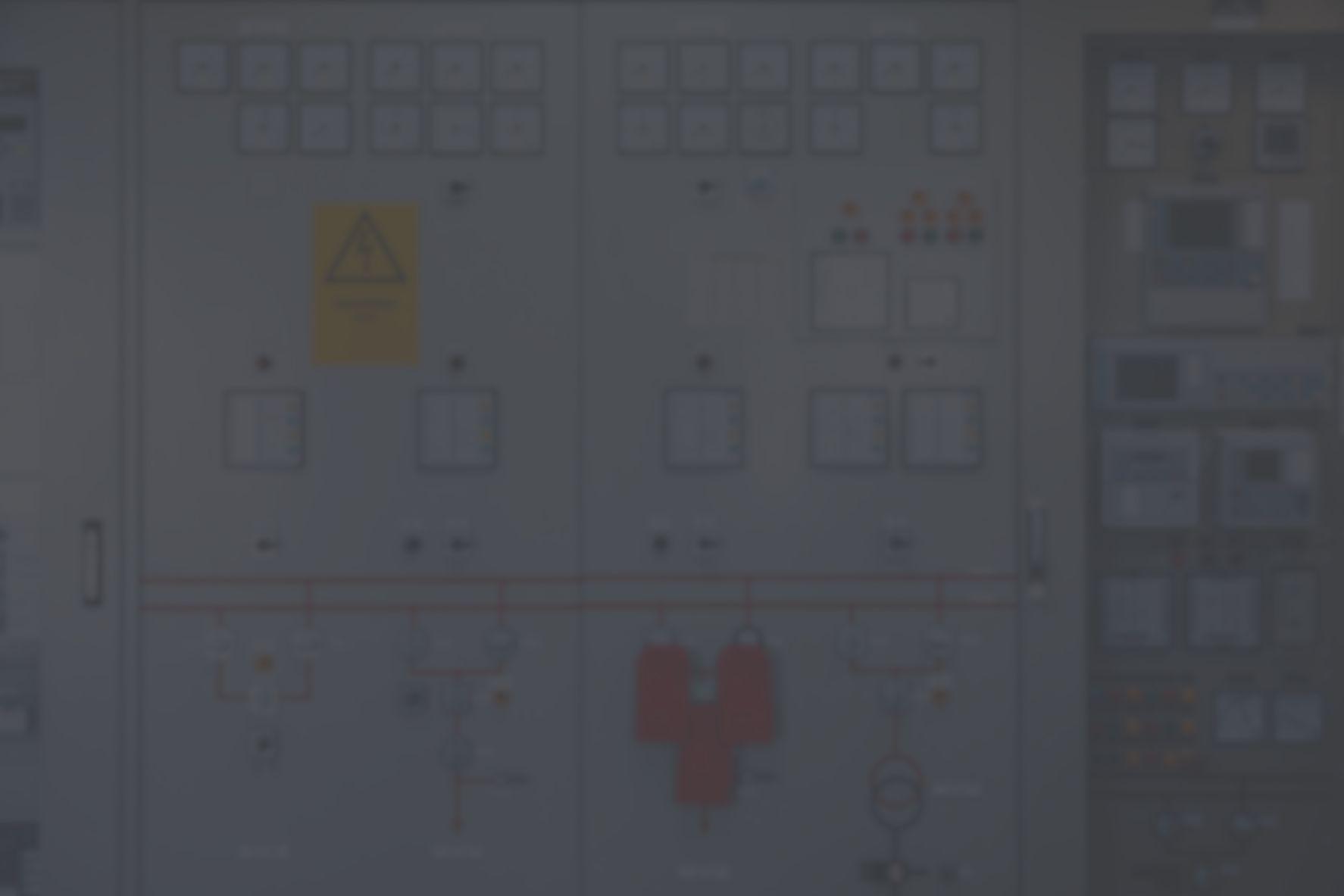
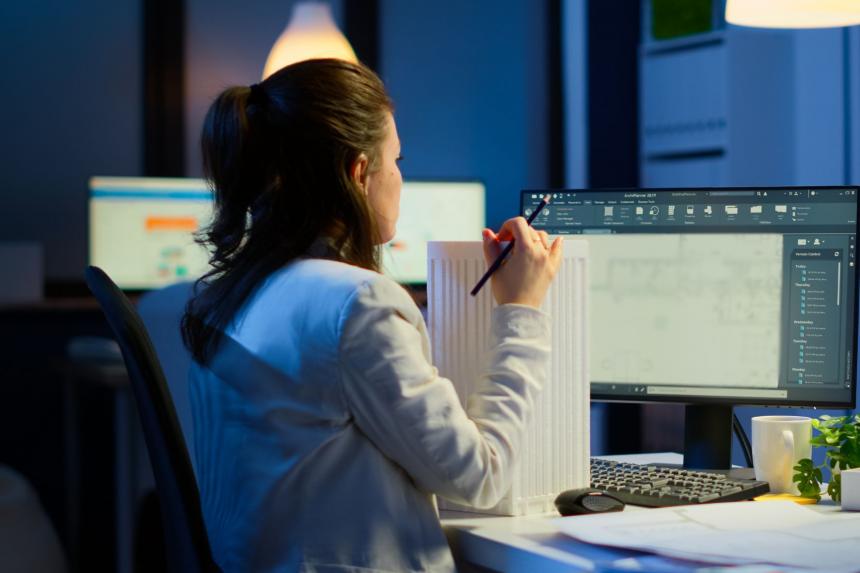
EPLAN as planning software
The EPLAN planning software enables the digitalization and automation of planning and production processes in control cabinet construction. With functions such as automated circuit diagram creation, the integration of IoT data and the direct connection to milling centers such as Perforex, EPLAN enables complex requirements to be implemented precisely and efficiently. The digital twin, which can be created in EPLAN, also optimizes maintenance and operation by integrating real-time data from IoT sensors and thus supporting predictive maintenance.
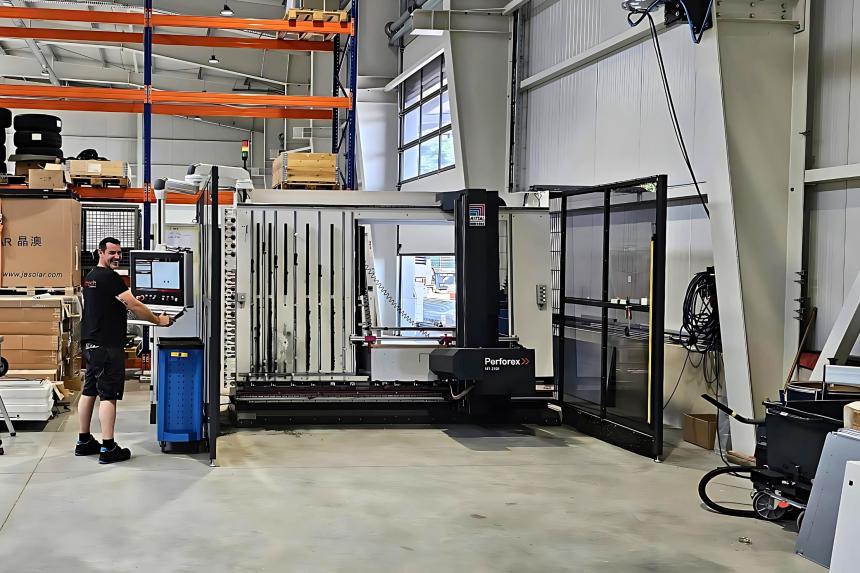
Precision and efficiency with the Perforex Milling Terminal
The Perforex Milling Terminal is a state-of-the-art machining center specifically designed for the precise manufacturing of control cabinet components. It offers the ability to machine front panels, housings and control cabinets quickly and accurately. The benefits include high machining precision, the flexibility to efficiently implement design changes and time savings through automated processes. The terminal can be seamlessly connected to planning software such as EPLAN so that manufacturing data such as drilling patterns, milling paths and material lists can be transferred directly. This integration minimizes manual errors and speeds up the transition from planning to production.
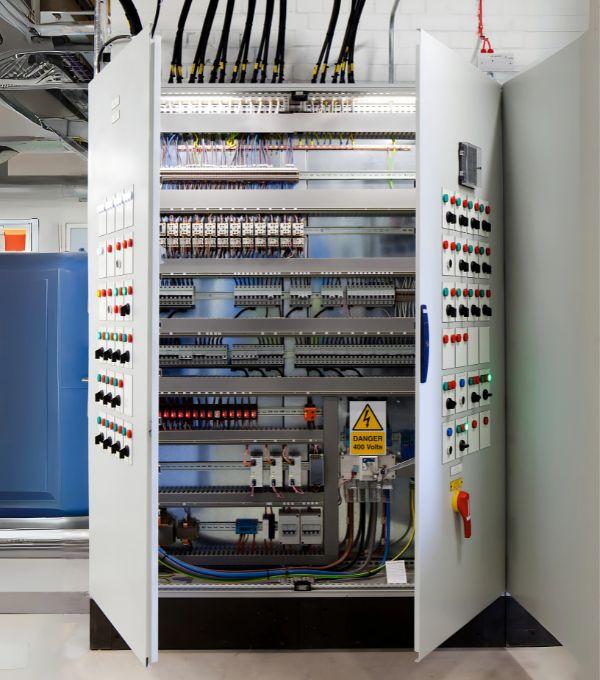
Flexibility in modern control cabinet construction
Control cabinet construction has developed into a highly flexible manufacturing process that responds to the individual requirements of different industries. Modular control cabinets enable rapid adjustments and extensions without having to rebuild the entire system. This is particularly advantageous in dynamic production environments in which machines and systems are frequently converted or extended. In addition, the use of standardized modular systems enables more efficient warehousing and facilitates maintenance, as spare parts are available more quickly. Flexibility thus becomes a key factor for future-proof control cabinet solutions.
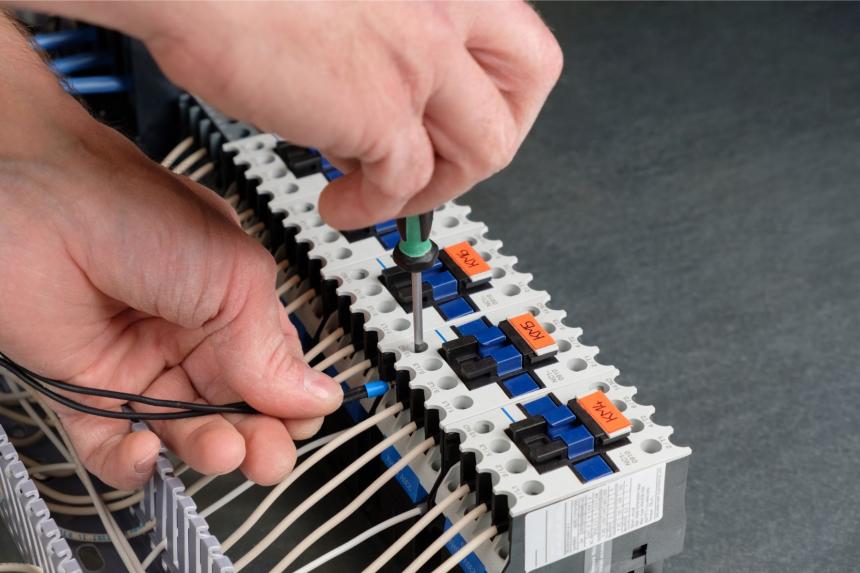
Optimization of wiring and cable assembly
In modern control cabinet construction, efficient wiring and cable assembly are of crucial importance for the reliability and functionality of the electrical systems. By using specialized planning software tools and CAD systems, the wiring is precisely tailored to the specific requirements of the control cabinet, which enables precise documentation and minimization of sources of error. The cable assembly itself is increasingly carried out in automated processes in which prefabricated cable harnesses are cut to the exact length and cross-section as required and equipped with suitable connectors. These pre-assembled cable harnesses reduce assembly effort and ensure high processing quality and improved operational reliability.
Conclusion - Opportunities and challenges in modern control cabinet construction
Control cabinet manufacturing has evolved significantly through the integration of advanced technologies such as IoT, Industry 4.0 and automated manufacturing processes. These innovations not only offer the opportunity to make the entire development and production process more efficient and precise, but also to significantly increase the flexibility and maintainability of the systems. Digitalization enables predictive maintenance, optimized commissioning and more sustainable production, which leads to increased efficiency and a longer service life of the systems.
Nevertheless, digital change also brings challenges. Integrating different systems and ensuring the compatibility of hardware, software and data standards requires extensive specialist knowledge and careful planning. In addition, companies must invest in training their employees in order to keep up with the new technologies and their potential.
Despite these challenges, modern developments in control cabinet manufacturing offer enormous potential to further optimize processes and lead the industry into an increasingly networked and intelligent future. Those who recognize these opportunities and take the right steps can position themselves as pioneers in a dynamic and promising market.
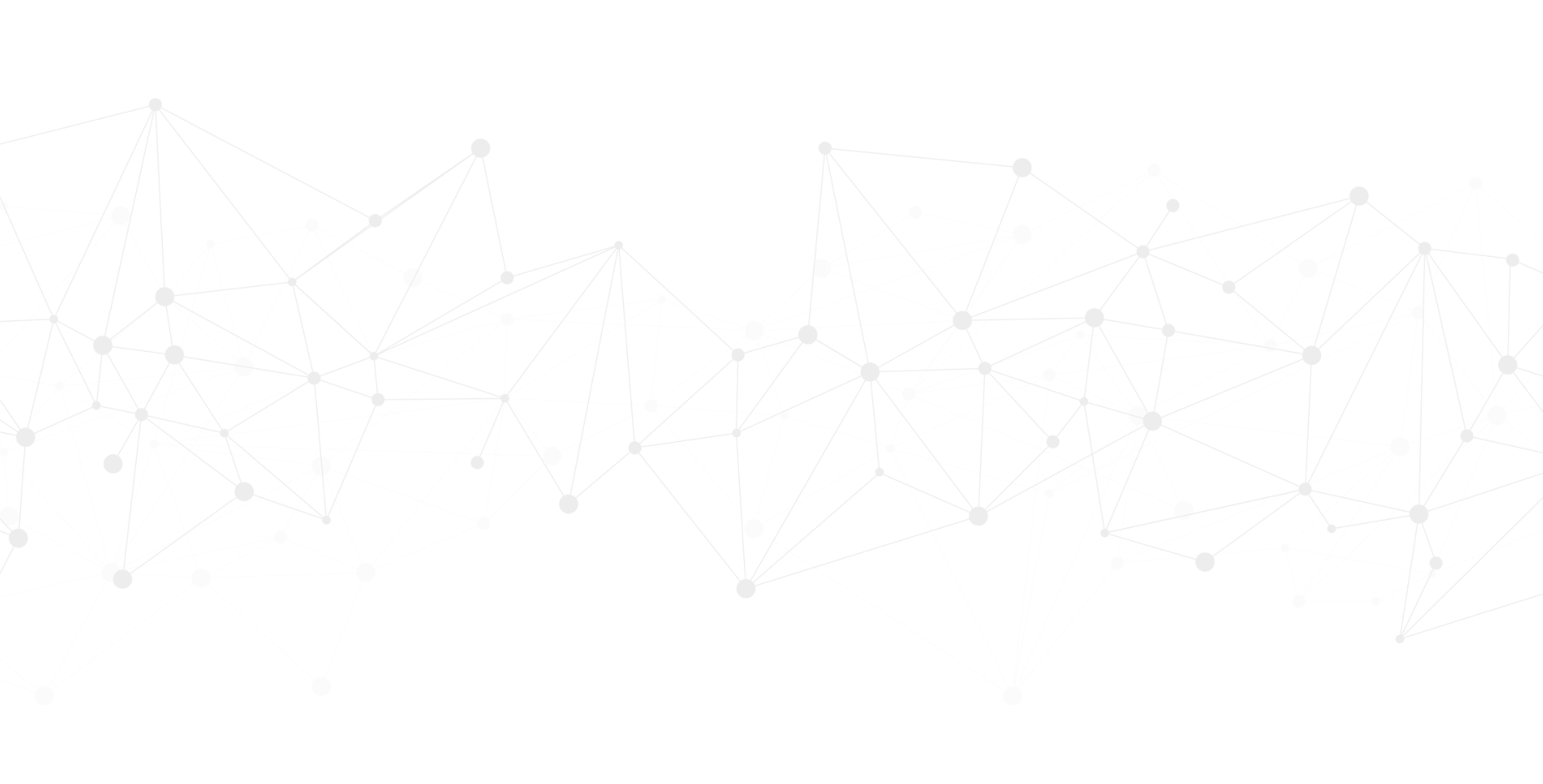
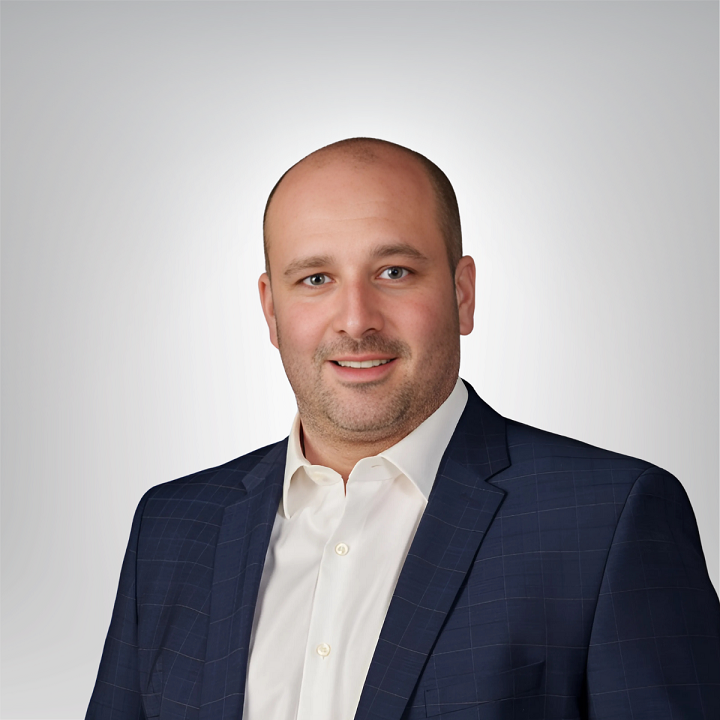
„Control cabinet construction is undergoing rapid change – that’s why we invest specifically in modern technologies and the continuous training of our employees in order to always offer our customers state-of-the-art solutions.”
Contact us
With our know-how in the areas of plant engineering and electrical engineering, the necessary human resources and a global network, we are ready for your project!
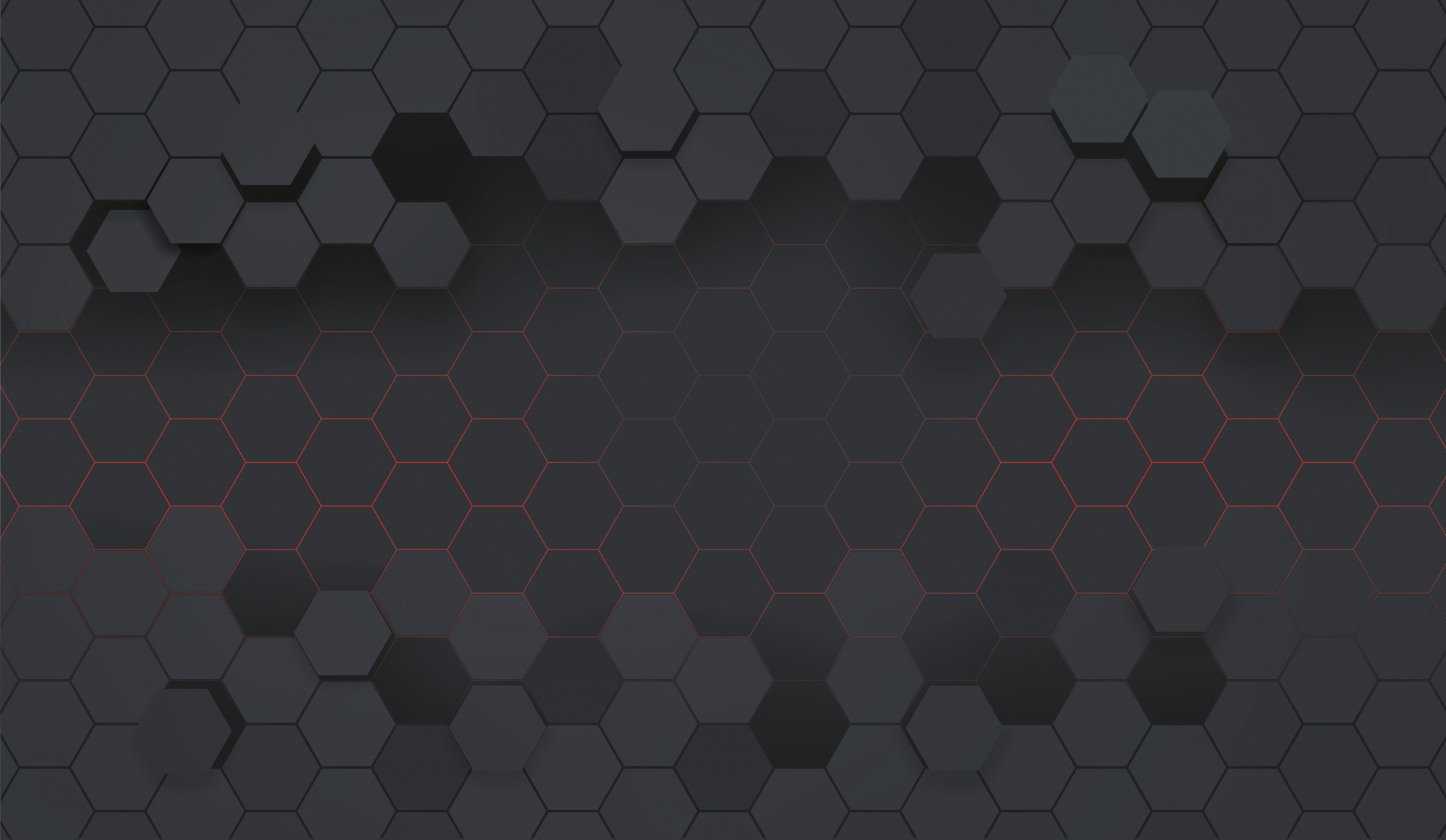