In plant engineering, choosing the right maintenance strategy is crucial to maximizing the availability and reliability of equipment. Equipment such as high-bay warehouses, conveyor systems or production machines must function smoothly to meet the requirements of end customers. In recent years, modern maintenance technologies have developed rapidly and there are now a variety of approaches to ensure the operation of equipment. This article highlights some of the most important modern maintenance strategies in plant engineering and explains how they can ensure the long-term efficiency and reliability of equipment.
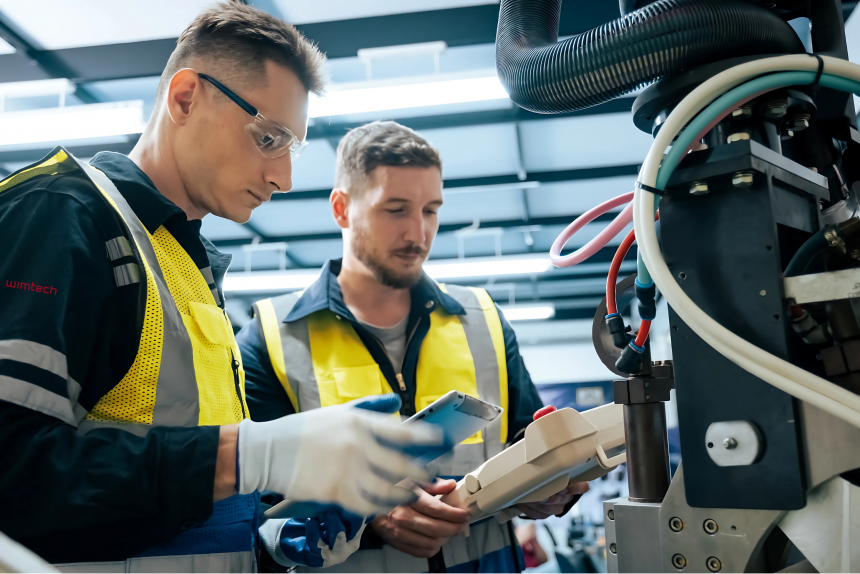
Reactive maintenance: Intervene when needed
Reactive maintenance (corrective maintenance) is a traditional method where action is taken only after a failure or malfunction has occurred. This may be useful in less critical applications as there are no regular maintenance costs . However, this approach carries the risk of unexpected shutdowns which can lead to longer downtimes. In some cases, reactive maintenance may be an acceptable solution, especially when the costs of a preventative strategy would be too high. However, the risk of a sudden failure must always be weighed against the risk.
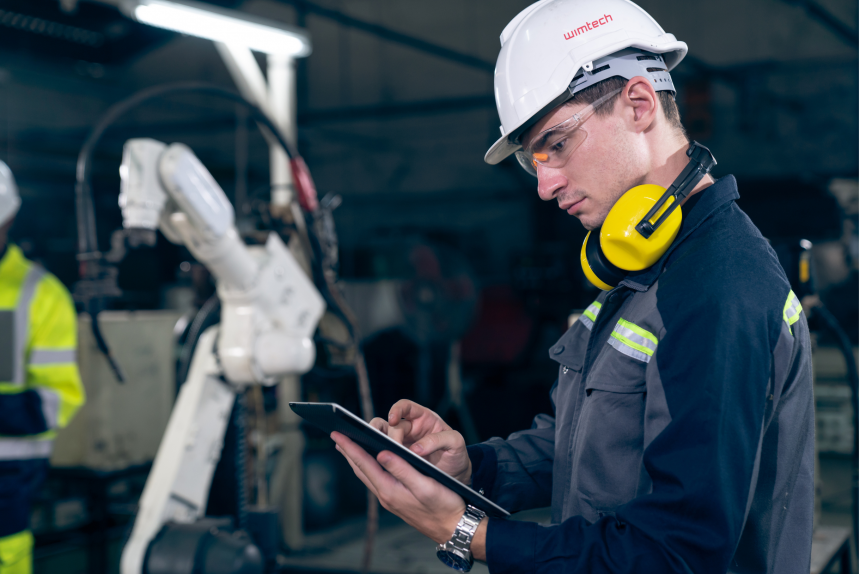
Preventive maintenance: regular inspections
Preventive maintenance is based on a fixed maintenance plan in which systems are checked and maintained at regular intervals . The aim is to prevent failures before they occur by carrying out maintenance measures based on time or usage . This approach offers a high level of reliability as regular checks ensure that wear and tear is detected and remedied in good time. For plant construction, this means a clear structure and plannable maintenance costs . However, it can happen that unnecessary maintenance work is carried out if the machines are still in good condition despite the set time.
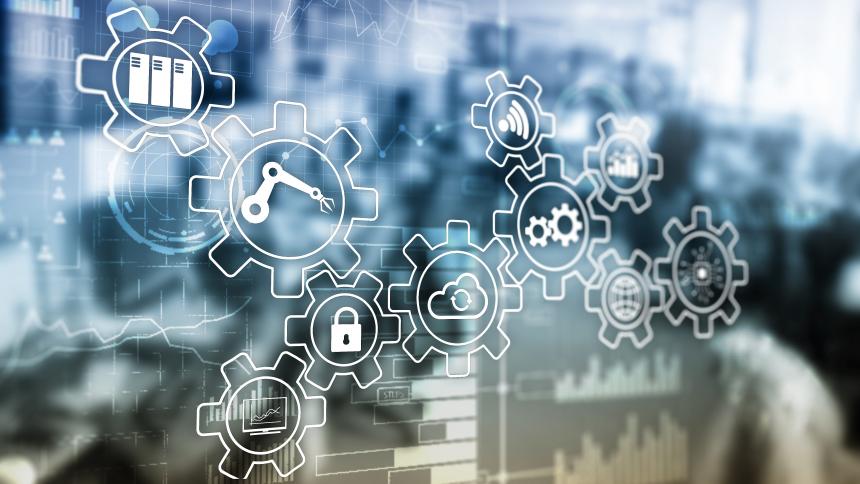
Predictive Maintenance: Predictive Maintenance through Data Analysis
Predictive maintenance is a modern approach based on the analysis of real-time data . Sensors are used to continuously monitor the condition of the machines and to make predictions about when a malfunction or failure is likely . This enables targeted maintenance that is only carried out when it is actually needed. Predictive maintenance has the potential to minimize downtime and maintenance costs because maintenance is only carried out when it is necessary. However, this data-based approach requires the installation of monitoring systems and appropriate software to analyze the data. For complex systems, this can offer significant benefits in the long term.
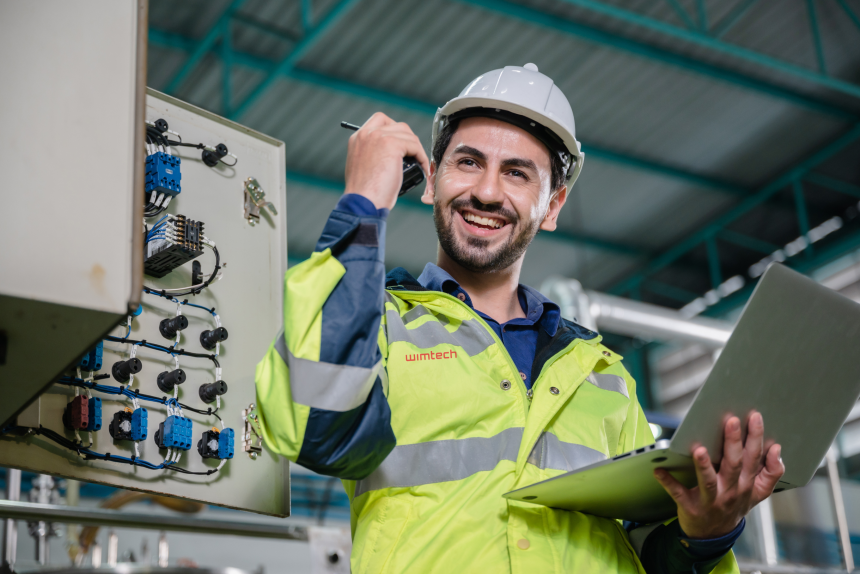
Condition-based maintenance: Maintenance according to machine condition
Condition - Based Maintenance (CBM) is an approach in which machines are monitored or inspected at regular intervals to assess their current condition . As soon as certain limit values are exceeded - for example in vibration or temperature measurements - maintenance is carried out. In contrast to predictive maintenance, CBM is not based on forecast models but on the current condition of the system . This approach is particularly useful when certain parameters can be reliably measured and allow direct conclusions to be drawn about wear.
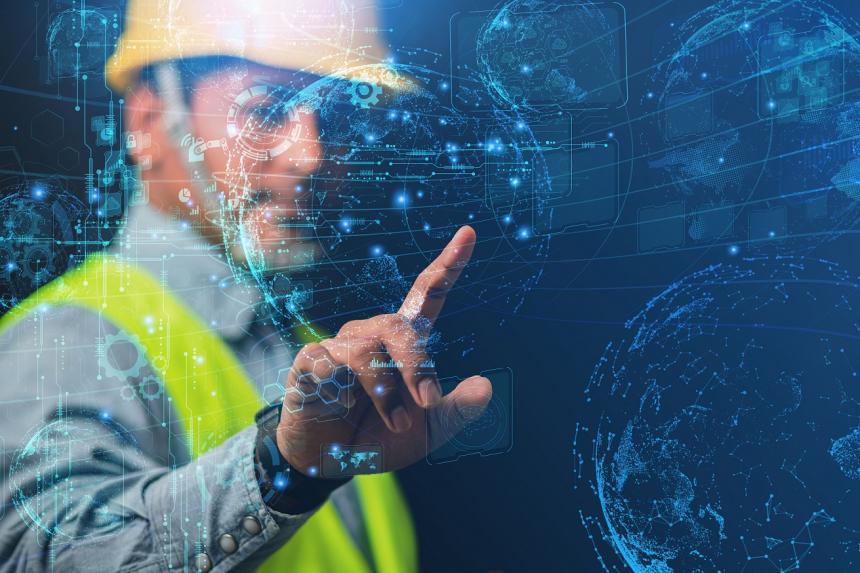
Remote Maintenance: Maintenance from a distance
The increasing digitalization makes it possible to carry out maintenance tasks remotely more often . Machines can be monitored via the Internet or an intranet and in some cases even maintained directly from a distance. In combination with predictive maintenance, problems can be identified and resolved more quickly without a technician having to be on site. Remote maintenance is particularly attractive for systems that are difficult to access or geographically dispersed . This saves time and money, as travel is no longer necessary, and enables a faster response to potential problems.
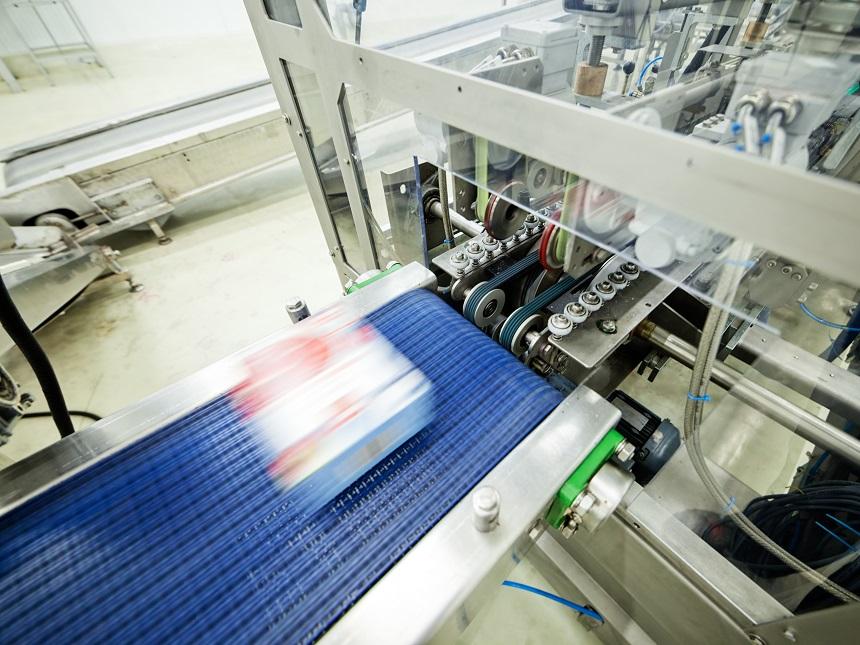
Total Productive Maintenance (TPM): Holistic approach
Total Productive Maintenance (TPM) goes a step further and considers maintenance as an integral part of the entire production process . TPM not only involves specialized maintenance technicians, but also machine operators take on simple maintenance tasks. The goal is to resolve minor problems at an early stage and maximize overall equipment effectiveness (OEE). TPM promotes a culture of continuous improvement and relies on the cooperation of all those involved to maximize machine availability and minimize downtime.
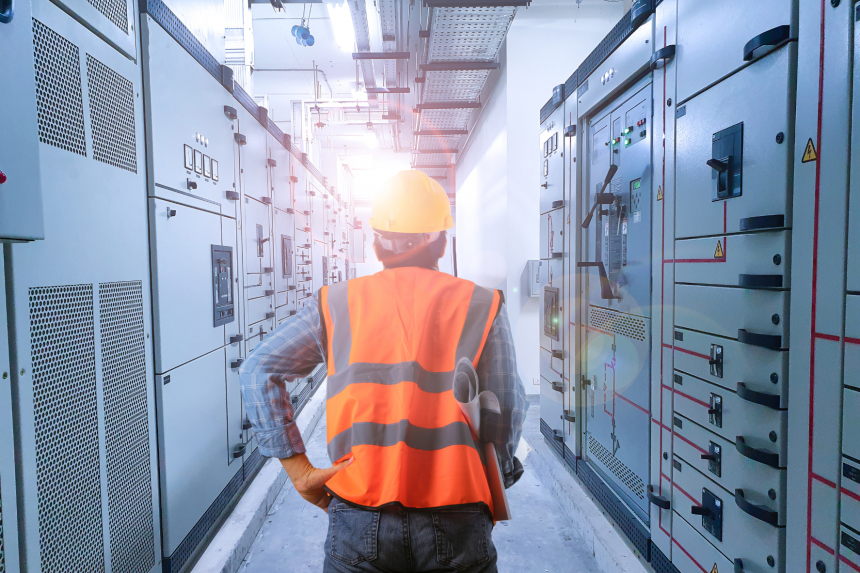
Reliability-Centered Maintenance (RCM): Maximum Reliability
Another modern approach is Reliability-Centered Maintenance (RCM) . This involves identifying the best maintenance strategy for each component of a plant . RCM combines elements of preventive , condition-based and reactive maintenance . The goal is to minimize the probability of failure while optimizing operating costs . RCM is often used on critical assets where downtime could have significant financial consequences . Analysis of the failure modes and potential impacts enables a tailored maintenance strategy for each asset.
Conclusion - Choose the right maintenance strategy
Modern maintenance strategies offer a wide range of options for maximizing the reliability and availability of systems in plant engineering . Whether preventive , condition-based , predictive or reactive maintenance – the choice of the right strategy depends on the specific requirements of the systems and the objectives . Technological advances, particularly in the area of data analysis and sensor technology, have led to new approaches such as predictive maintenance and remote maintenance , which further improve efficiency and cost control. Nevertheless, more traditional methods such as preventive maintenance and TPM have not lost their importance . It is important for plant engineers not to leave the maintenance strategy to chance, but to carefully consider which approach will deliver the best results. Each strategy has its strengths and weaknesses , and often a combination of different approaches can promise the greatest success.
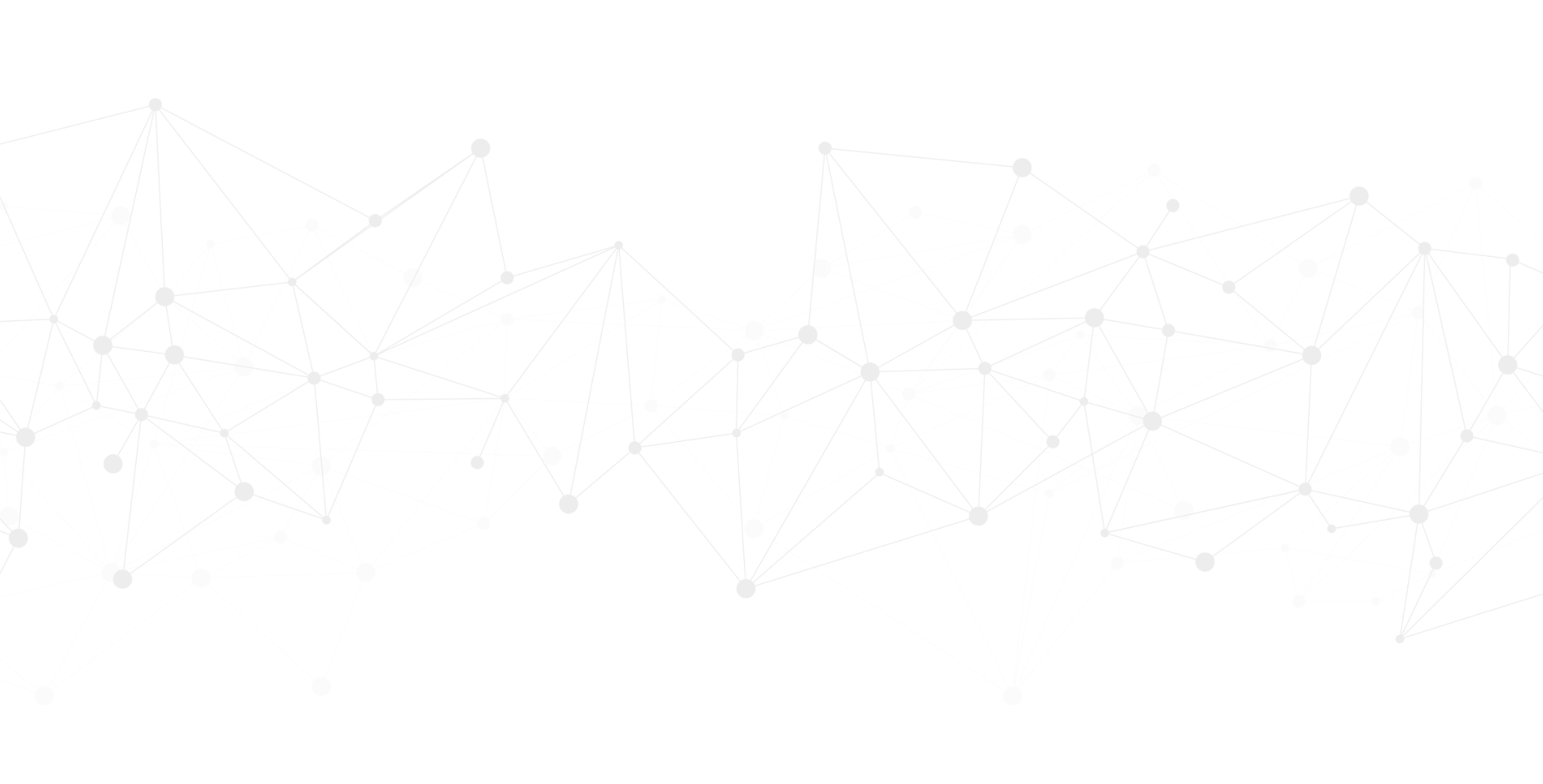
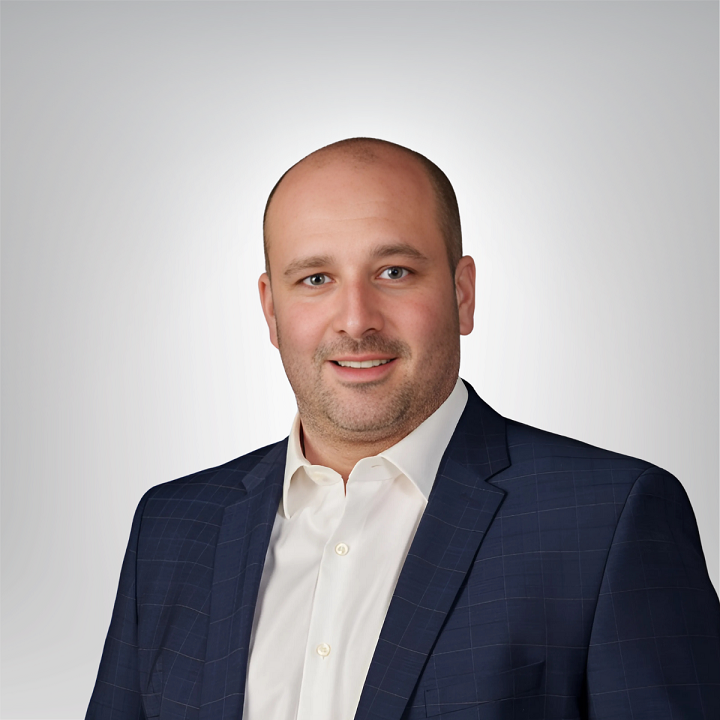
WIMTECH as a partner
We support our customers in the commissioning, service and maintenance of their systems and provide highly qualified specialists and modern equipment. Throughout the entire project, we follow our customers' specifications precisely and are optimally equipped for urgent assignments without long planning phases.
Contact us
With our know-how in the areas of plant engineering and electrical engineering, the necessary human resources and a global network, we are ready for your project!
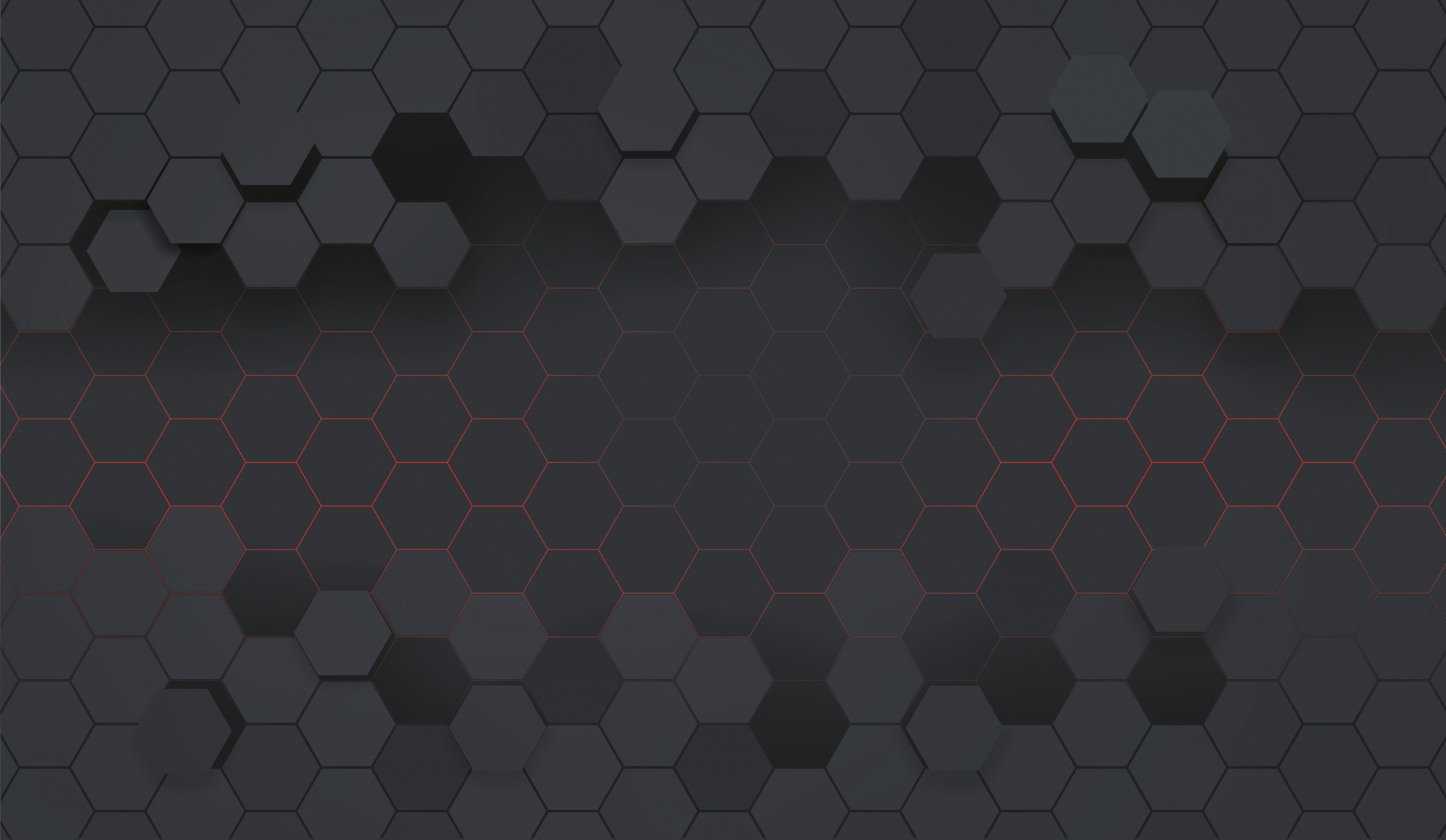