The shortage of skilled workers poses considerable challenges for plant construction. For globally operating companies such as WIMTECH, it is particularly important to recruit qualified specialists and retain them in the long term. Our fitters and project managers play a key role in the successful implementation of international projects. Through targeted investments in our employees, state-of-the-art technologies and the continuous optimization of our processes, we ensure that we work efficiently and deliver the highest quality even in a challenging market environment. In this article, we examine how WIMTECH meets these challenges.
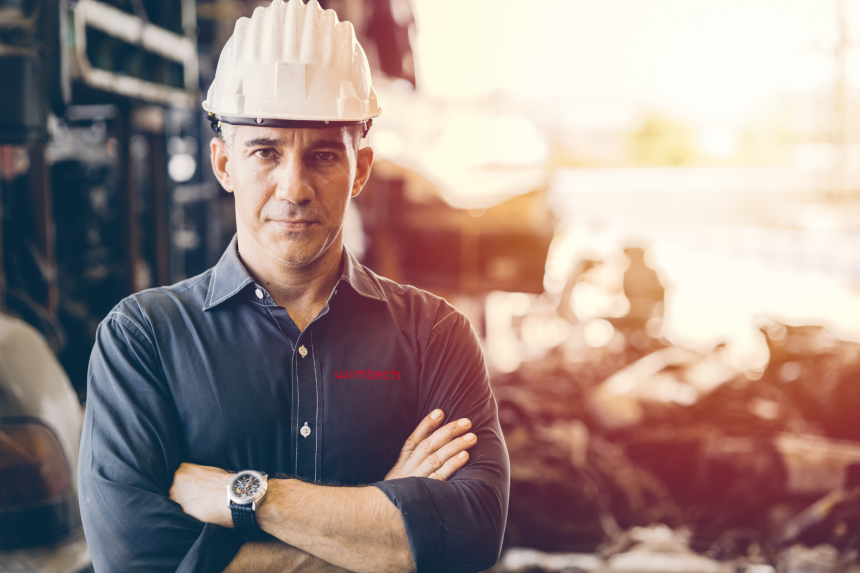
Long-standing employees as the cornerstone of the company
Our experienced fitters and project managers are the heart of WIMTECH. With their extensive know-how and many years of experience, they are essential for the successful implementation of our projects, especially in an international context. We value these valuable employees and create an environment that recognizes and promotes their expertise. Their in-depth experience in plant construction is an indispensable part of our success story.
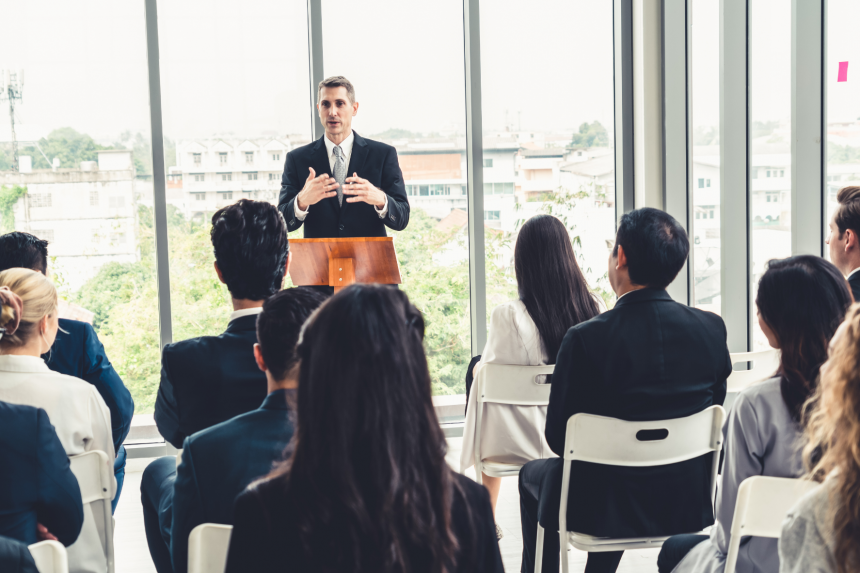
Continuous training and further education
In order to meet the requirements of international projects, we offer our employees regular training and further education. Our fitters and project managers receive ongoing training in the latest technologies and methods. In addition to technical training, this also includes training in intercultural skills and international project management to ensure that they are well prepared for the special challenges of global projects. This not only contributes to the quality of our projects, but also promotes the personal and professional development of our employees.
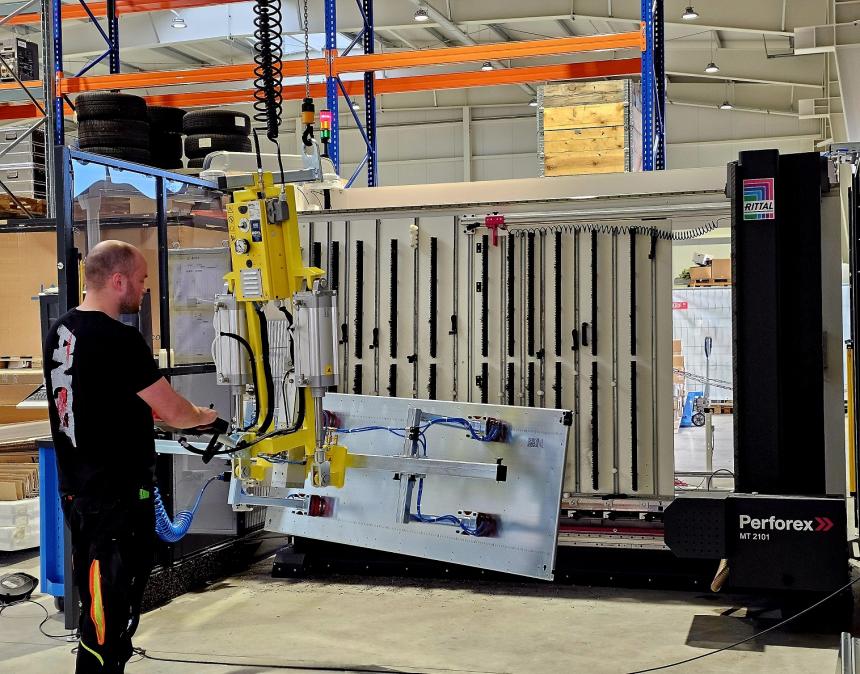
Modern tools and technologies
Our fitters and project managers are equipped with the latest tools and technologies that enable them to do their work efficiently and precisely - no matter where in the world they are working. We invest in sophisticated machines such as our Perforex milling center and modern cranes that not only make work easier but also increase the precision and quality of our projects. These technologies are crucial to meeting the requirements of our international projects and to providing our employees with the best possible support.
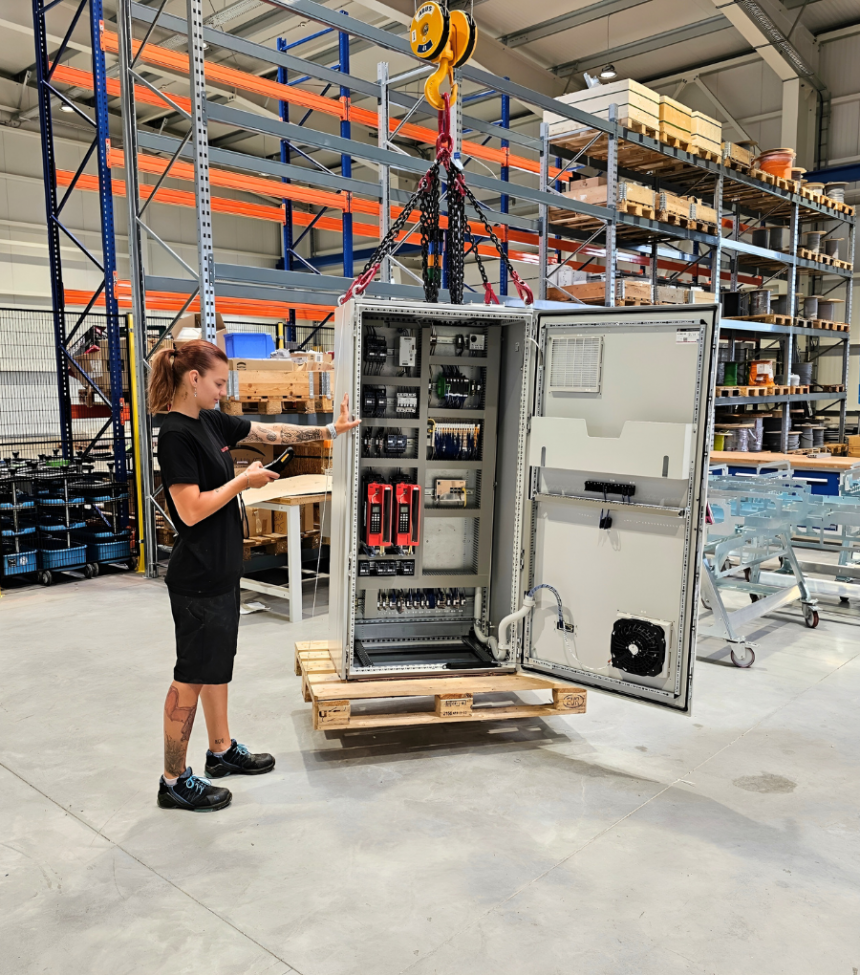
Investments in machinery to relieve the workload of the workforce and ergonomic workplaces
The health and well-being of our employees are our top priority at WIMTECH. Ergonomic work equipment and the correct design of the work environment are crucial to ensuring that our fitters, employees and project managers remain productive even under challenging conditions. In addition to training and equipping our employees, we invest specifically in machines and tools that reduce the workload of our fitters and workers while increasing efficiency. In our assembly hall or on international projects, where conditions are often demanding, our machines and tools make a decisive contribution to making work easier. The workstations in our offices are also ergonomically designed and are individually adapted to the needs of the employees. These investments help ensure that our employees stay healthy and motivated while at the same time being able to carry out their tasks with the highest level of efficiency.
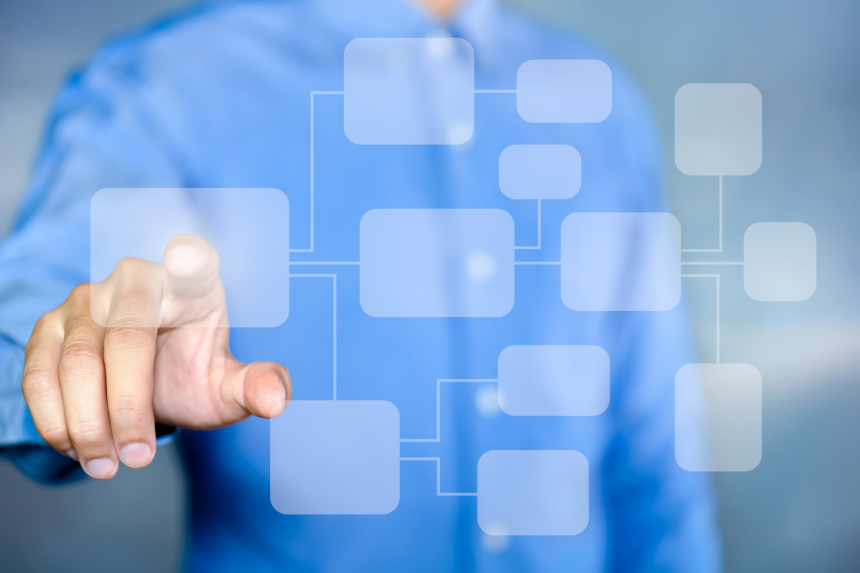
Continuous process optimization
Efficient processes are essential for project success, especially given the shortage of skilled workers. We continuously optimize our internal processes to ensure that our projects are not only completed on time and within budget, but also with the highest quality. By using lean management principles and state-of-the-art software for project planning and control, we can identify bottlenecks early on and make optimal use of our resources. These optimizations enable us to work more efficiently and meet the high demands of our customers. Clearly defined workflows and standardized processes not only ensure that projects run smoothly, but also relieve our employees and reduce the psychological pressure on projects with tight timelines.
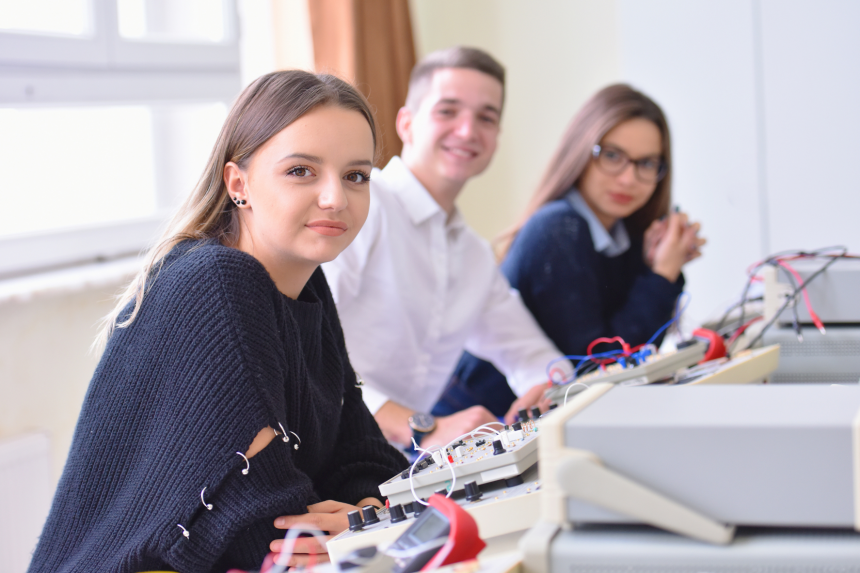
Promoting young talent and apprentices
In addition to supporting our existing workforce, we place great value on training young talent who want to specialize in international projects. Our training program is designed to involve young talents in practice at an early stage and to teach them the skills they need for a successful career in international plant engineering. Through practice-oriented training and close cooperation with our experienced fitters and project managers, we ensure that our know-how will continue to be passed on in the future.
Conclusion
The satisfaction of our employees is a decisive factor for the success of our projects. To promote this, we rely on an open communication culture and regular employee discussions in which 360-degree feedback plays a central role. These discussions help us to identify and respond to individual needs and concerns at an early stage. At WIMTECH, we work on an equal footing. Our flat hierarchies enable us to respond quickly and flexibly to the requirements and problems of our employees. Managers always have an open ear and are there to support their teams. This appreciative culture helps to ensure that our employees remain motivated and committed, which has a positive effect on the quality of our work and the success of the project.
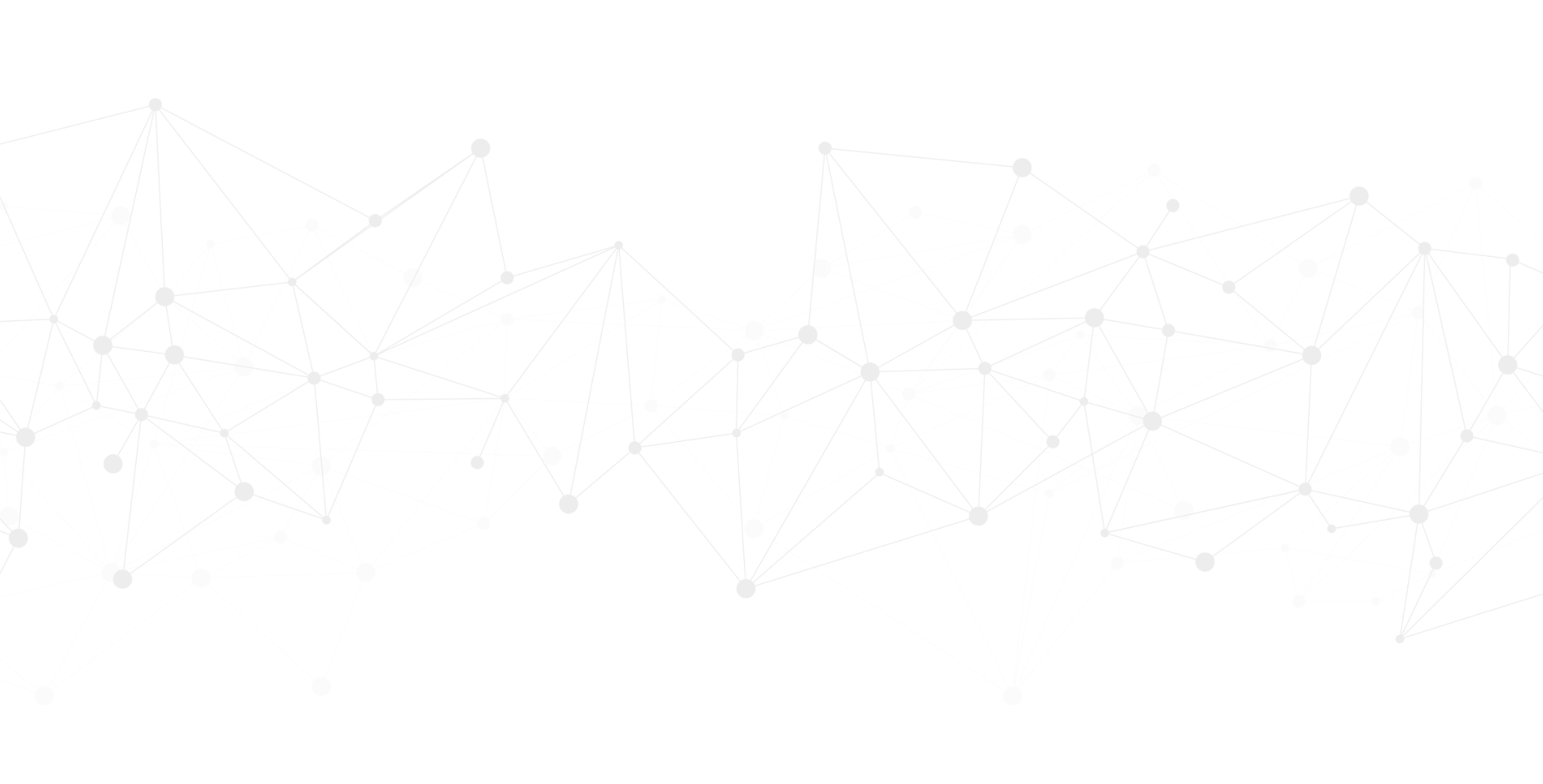
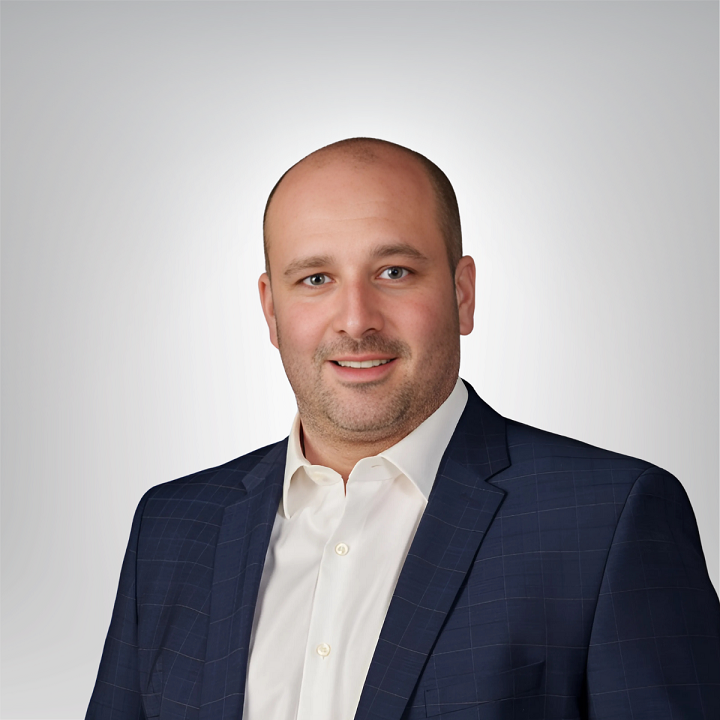
„Respect and communication on an equal level are standard for us, because money cannot buy passion or loyalty.”
Contact us
With our know-how in the areas of plant engineering and electrical engineering, the necessary human resources and a global network, we are ready for your project!
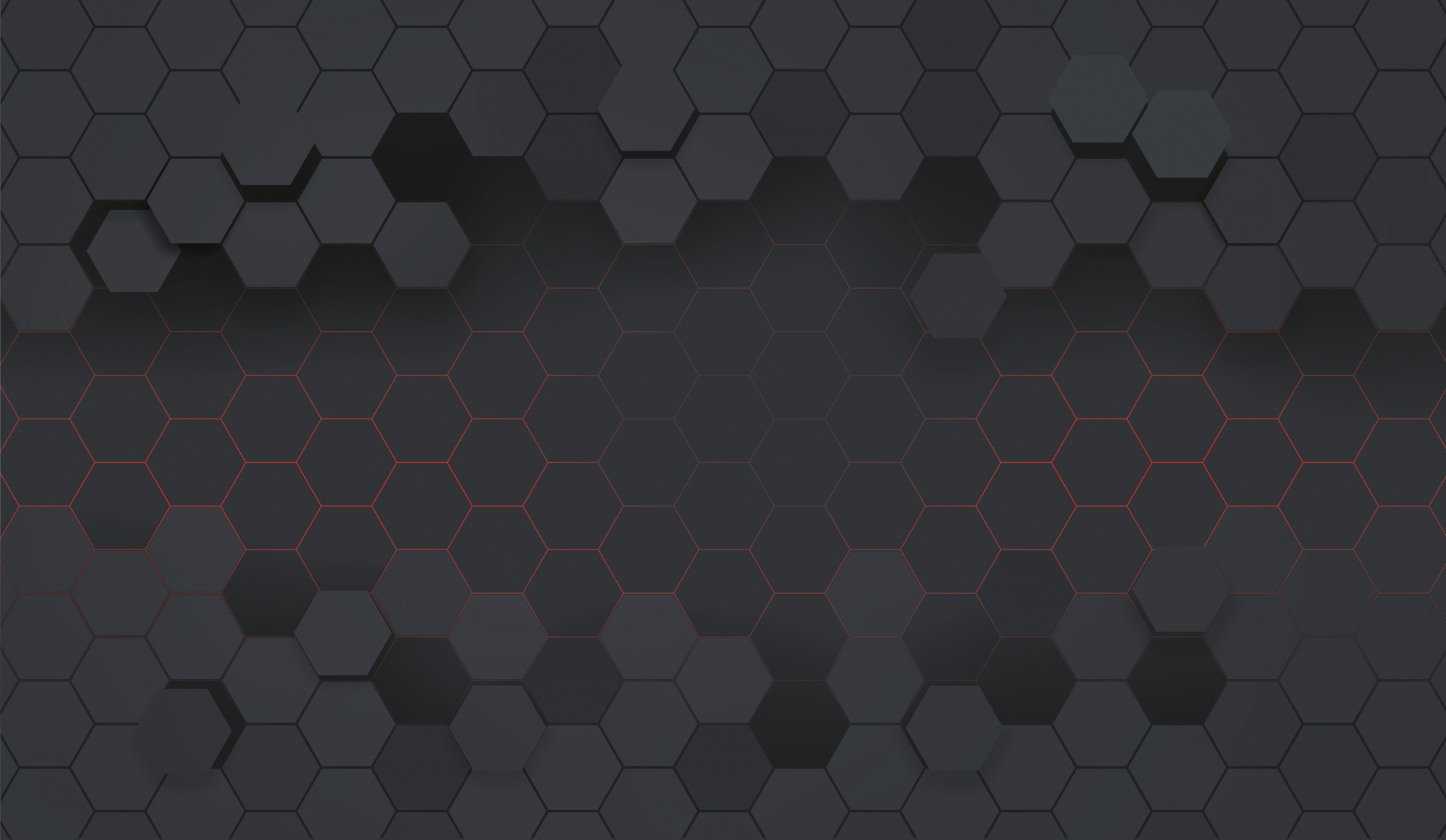